Machinery Needs Proper Lubrication
Lubrication is a vital component in the safe and efficient life span of any moving and rotating machinery. Getting a job done without machinery breakdowns saves money and downtime. One way to ensure that happens is to have all machinery working at optimum capacity with proper lubrication.
What are Lubricants?
Lubricants are oily or greasy substances applied to machinery parts that meet each other during operation. These are commonly a mix of base oil, which can be synthetic, mineral, or vegetable-based, and an additive to enhance the lubricant. Grease is another form and created by mixing a thickening agent with the base oil.
There are two different types of lubrication systems used, automatic and manual.
Where You Want it, When it's Needed
An automatic system provides lubrication to the machinery, usually while it is in motion, as and when required. The added advantage is that automatic lubrication practically guarantees the extended life of the equipment and lowers maintenance costs.
Manual Lubrication
This conventional method requires a technician to apply lubrication via a grease gun or similar tool and forces the temporary shutdown of equipment. The downside of manual lubrication includes potentially higher maintenance costs if the application is inconsistent in timing and amount.
Lubricants are necessary for the safe and effective operation of machinery and provide several benefits that reduce costs associated with breakdowns and equipment replacement.
Wear and Tear
Lubrication prevents wear and tear on the machinery by applying a thin oily layer or coating between two moving metal surfaces. Although each machine's surface appears smooth, they are both covered with microscopic asperities or tiny peaks that stick out and scrape against each other when in motion, causing friction, which in turn creates heat buildup. Lubrication prevents machinery wear and adds longevity by keeping the motion fluid and by dissipating heat.
Corrosion
By adding lubricant, machinery is also protected against rust and corrosion, sealing the components from contact with water and other erosive elements. Lubricants also latch onto and draw away unwanted harmful contaminants to filters and removal systems.
Keeping Things Cool
Friction between surfaces builds up heat, which in turn can lead to machinery burnout. Lubrication dissipates heat, cooling down machinery and keeping the operating temperature at the desired level.
Longer Life Expectancy
Using the proper lubricants and correct application by automatic or manual systems will give machinery a much longer life span and retain its productivity value. Lubrication should minimize friction, heat, and wear, as well as prevent corrosion and contamination. Action Supply Inc. is a leading source for machinery lubricants, meeting and exceeding industry standards. With the proper use of lubrication, the equipment can be relied upon to work for extended periods.
Down With Costs
When equipment fails, repairs are costly in more ways than one. Downtime, materials, and technician hours all add up. The cost of using lubricants is minimal in comparison and keeps machinery operation reliable and repairs to a minimum. In turn, this leads to increased productivity and revenue.
There is more involved in lubricants than might be expected. The importance of using the appropriate lubrication ensures machinery is at its most productive and energy efficient.
One of the biggest reasons for bearing failures, according to SKF, is due to a lack, or incorrect application, of lubricants. Application and using the appropriate lubrication are both necessary for increasing equipment productivity and reducing potential breakdowns.
Contact Action Supply Inc. to answer your questions regarding the proper lubricant for your machinery.
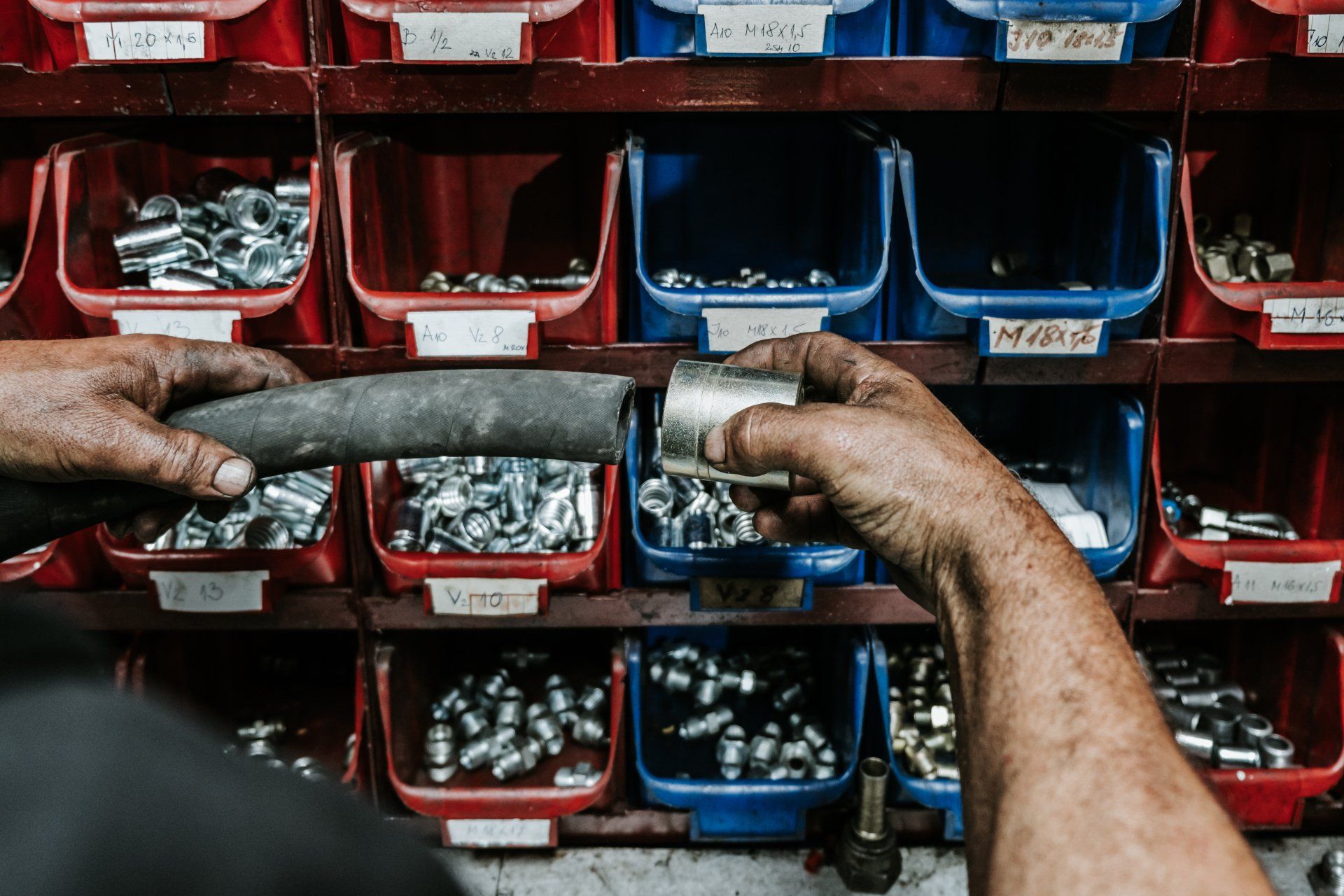
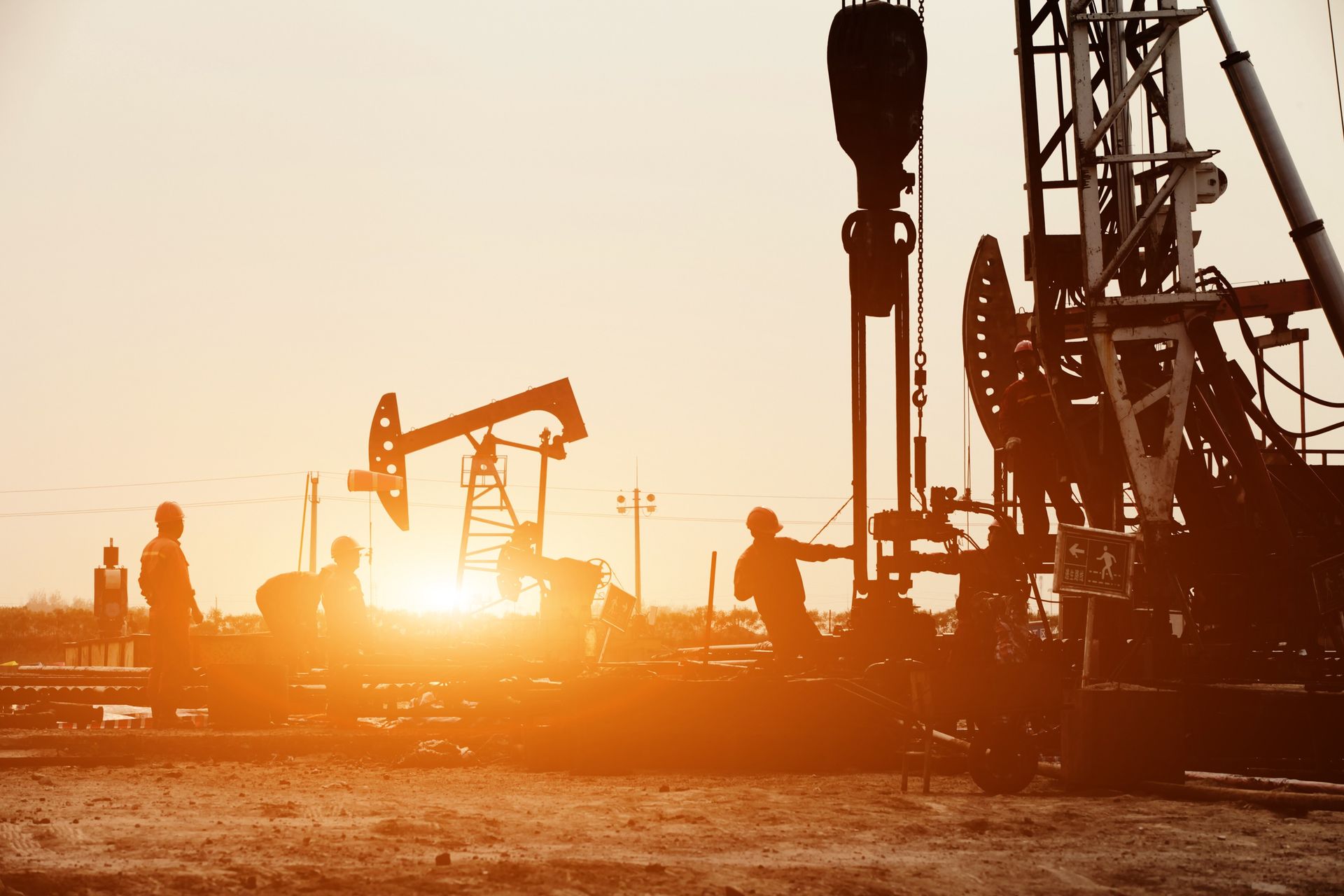