How To Manage And Optimize Spare Parts Inventory
From manufacturing equipment to fleet maintenance, having spare parts at your disposal is critical to keeping your most essential equipment functional at all times. The problem? Businesses with disorganized spare parts systems can end up with fewer components than they need at a given time.
This shortage can complicate matters should you not have the components you need to keep your business operational. Fortunately, all that’s required to avoid this issue entirely is to better manage and optimize your spare parts inventory. This guide will dive into a few helpful tips to make spare parts management seamless.
Label Your Parts and Develop a Process for Removal
Arguably two of the most significant issues that those dealing with spare parts inventory management face are not properly labeling parts and not creating a system to track their removal.
By labeling, we don’t mean that you need to inform your employees about what these items are (although this is helpful). Instead, you need a labeling system that results in efficient inventory management. Two great systems include the ABC system (highest, intermediate, and lowest consumption value, respectively) and the XYZ system (little variation and reliable forecast, some variation, most variation, respectively).
Of course, properly labeling does little if employees do not have a system they can follow when removing and tracking parts. So, create a standard work order process and train employees so that they know to file a formal work order and how the system functions. This training will eliminate any issues you’re currently facing on this front.
Understand Your Buying Cycles and How Much Inventory You Have
Spare parts are necessary, but the last thing you want to do is order too much (or little) or cut deep into your profits to keep these items on hand.
To better address the first part, you can use sawtooth diagrams and create a visualization of when you replenish your spare parts inventory and how quickly it dwindles over time. Then, with further insight into your purchasing habits and how often you go through spare parts, you can better prepare for the future.
To ensure you’re not spending too much on inventory, you can use a formula for support. The economic order quantity is designed to help you minimize inventory holding and related costs. You can calculate the economic order quantity using the following formula: EOQ = square root of 2(setup costs)(demand rate) / (holding costs).
Conduct Regular Cycle Counts and Occasional Total Inventory Counts
Managing your spare parts inventory involves more than just labeling products and developing systems around them. Checking in to see what you have on hand and ensuring that your new systems are functioning as expected is also crucial to the process.
Total inventory counts may be conducted from time to time. However, cycle counts can be useful as they’re not disruptive. These types of counts are audits of a group of inventory parts to ensure that the amount of items in your inventory matches what you have in your system. You may even develop a regular schedule for these types of checks!
Get Reliable Inventory Management Support From Action Supply
Need help managing your spare parts inventory? Action Supply is here to help! Our account representatives dedicate themselves to supporting your business by offering fully-managed inventory services. So, keep your business covered and your inventory full of the parts you need when you need them by contacting us today!
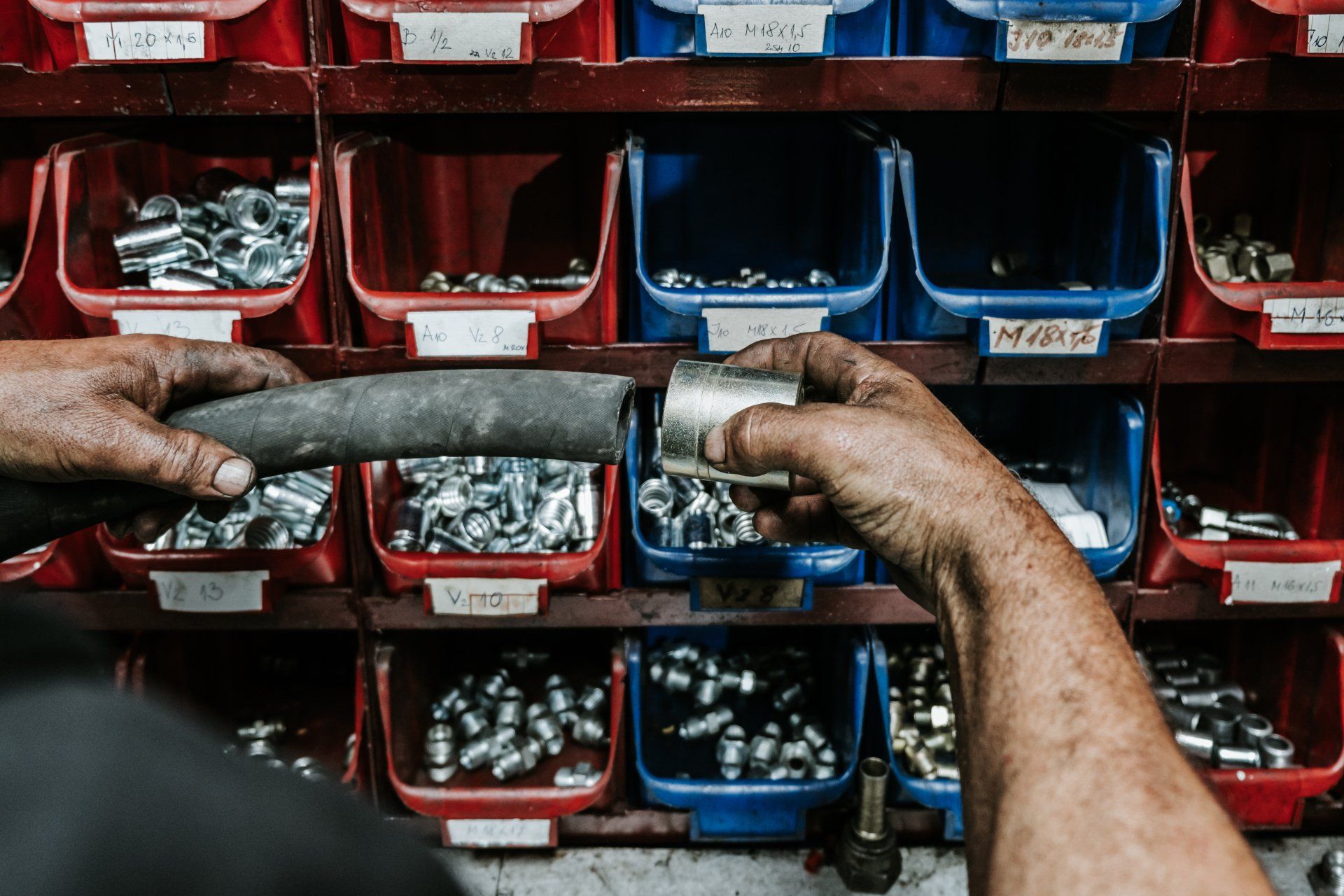
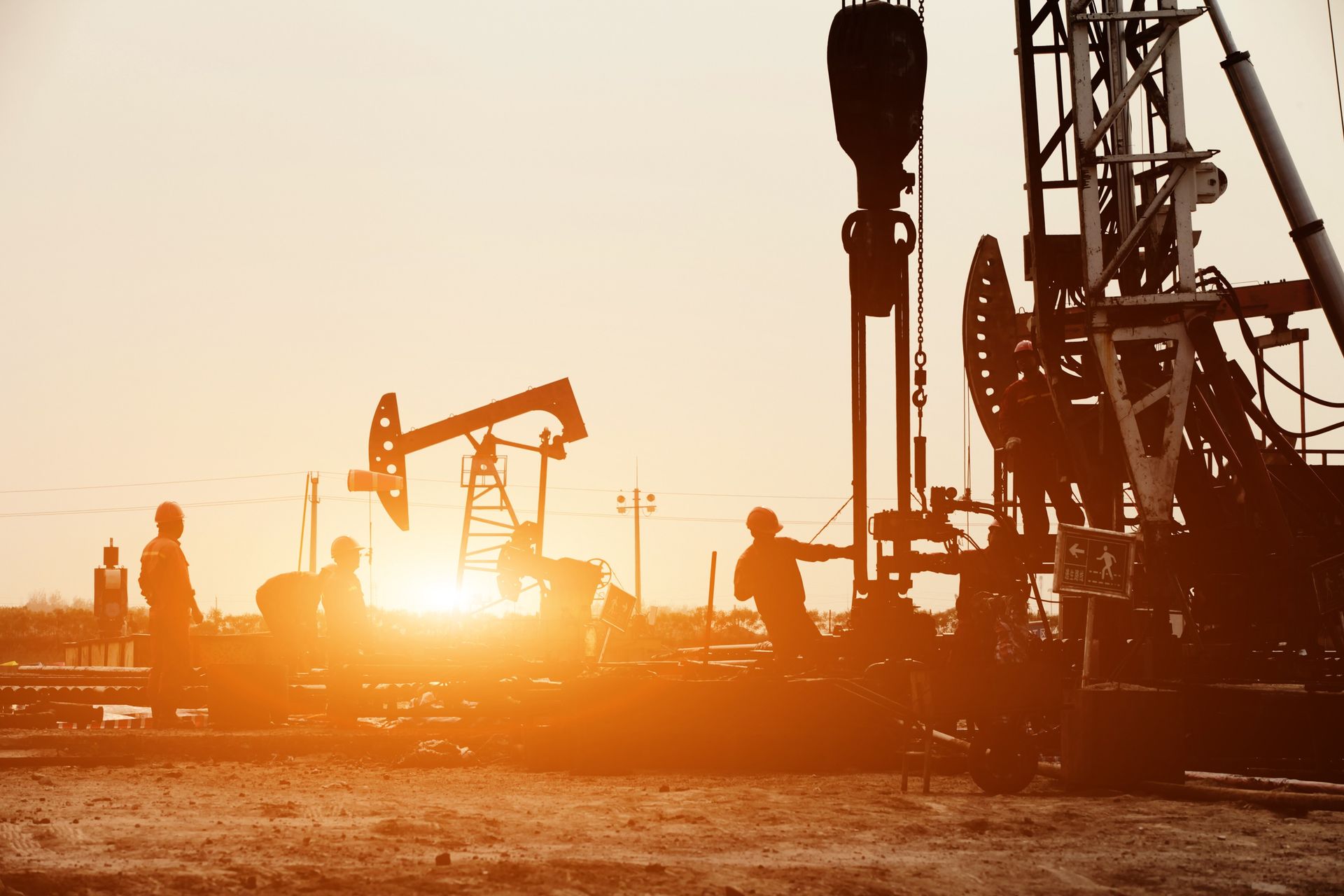