5 Common Mistakes in Heavy-Duty Truck Air Brake System Inspections and Adjustments
Despite the growing interest in Electronic Braking Systems (EBS), Anti-lock Braking Systems (ABS) continue to be the preferred choice for heavy-duty trucks due to their reliability. Here are some common mistakes made during air brake system inspections and adjustments with tips on how to
Neglecting Regular Inspections
Regular inspections are critical to detect wear and tear before they become costly breakdowns. Procrastinating on this critical task can lead to accidents, injuries, and other risks.
You should visually inspect the air brake system every three months and more thoroughly on a schedule according to the manufacturer’s recommendations. Plan for extra visual inspections if your fleet is exposed to extreme weather, severe temperatures, or other environmental hazards.
Improper Adjustment of Brake Components
Improper adjustments can occur due to a lack of understanding of the correct adjustment procedures or the use of incorrect tools. For example, an imperfect slack adjuster can lead to excessive brake shoe wear or inadequate braking force.
Make sure your crew follows the manufacturer's guidelines and uses the right tools for adjustments and repairs. A minute saved with a rushed job can cost many days' worth of issues later.
Ignoring Manufacturer Specifications
Each brake system has specific manufacturer specifications and guidelines. Doing things like using incorrect brake linings or failing to maintain the recommended air pressure can lead to decreased performance and increased risk of brake failure.
Always refer to the manufacturer’s manual and adhere to the specified maintenance practices.If you are unsure if a substitute part will work for your fleet vehicle, contact hardware supply experts to discuss your options.
Failing to Check Supporting Hoses and Valves
Air leaks in the brake system can severely affect braking performance. Common areas where leaks might occur include the air hoses, valves, and connections. During inspections make sure to:
- Check for cracks, bulges, and other deformities in the hoses
- Gently pinch the hoses to check for blisters and soft spots that indicate internal damage
- Check joints, valves, and connectors for signs of corrosion and loose connections
- Take care that all tubes and parts are clean during repairs and replacements. Any debris that makes its way in is not likely to come back out
- If you suspect a leak, cover the hose with soapy water and look for bubbles.
Replace any faulty parts early on to avoid more costly repairs later. A customized inventory management service can help you avoid long back orders and delays.
Overlooking the Air Dryer and Filters
The air dryer and filters play a critical role in maintaining the quality of the air within the brake system. Moisture and contaminants in the air can cause corrosion and damage to the brake components, especially in humid areas like the Gulf Coast.
The staff of Fleet Magazine recommend, “Drivers and fleets should always monitor the quality of the air in their service tanks to ensure air dryers are functioning properly. If excessive moisture—or oil mixed with water—is present in an air system, the air dryer’s cartridge may need to be replaced.”
Regularly checking and replacing the air dryer cartridge and filters can prevent moisture buildup and ensure the longevity of the brake system. Refer to the manufacturer’s appropriate data sheet for the best intervals.
Let Action Supply Help You Maintain Your Fleet
Whether you need the gold standards in
fleet maintenance parts or robust inventory management, we are committed to providing you with the highest quality customer care. Our inventory experts will work hard, earn your trust, and help you get the job done right.
Contact us today to discuss your fleet maintenance needs.
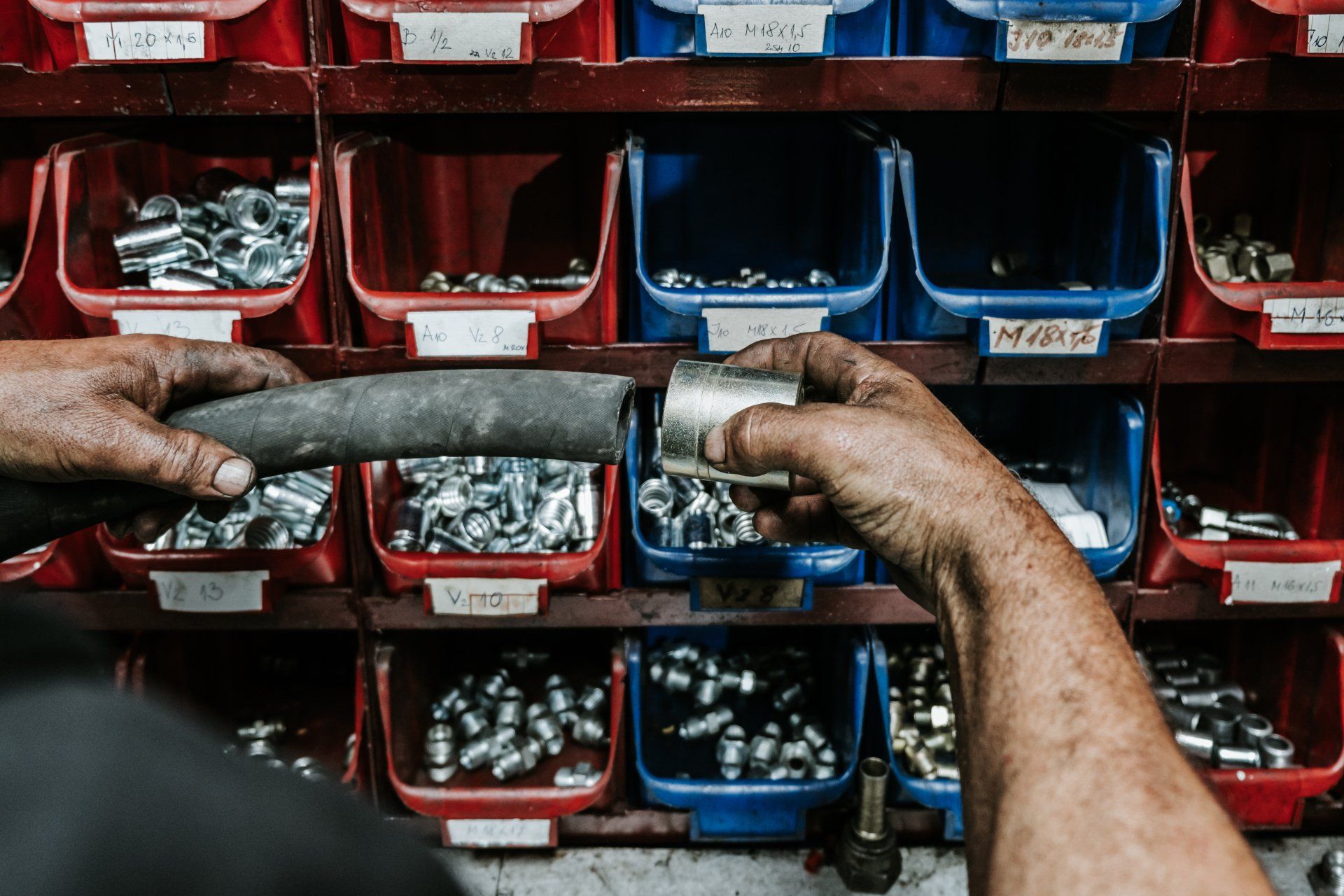
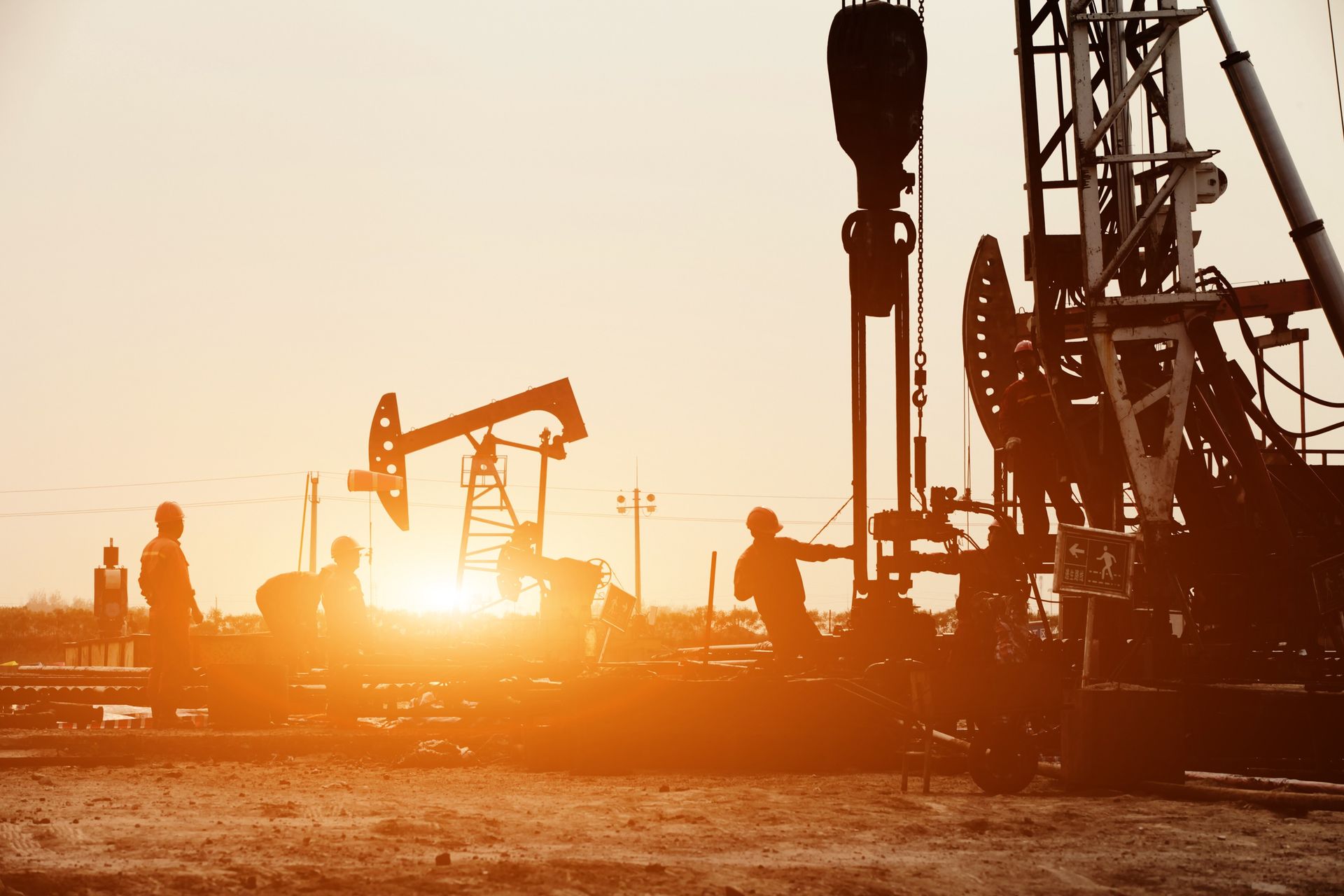