How to Minimize Hydraulic System Contamination
Contaminated hydraulic fluid can result in abrasive wear, corrosion, and diminished efficiency of hydraulic components, and it is one of the leading causes of hydraulic system failure. Here are some tips from our pros on how to minimize the effects of contamination on your hydraulic system.
How Your Hydraulic Fluid Becomes Contaminated
Before we go into tips, it is helpful to know where these contaminants come from. Some of the most common include:
- Refilling the system with used or low-quality hydraulic fluid
- Refilling the system from a container contaminated during multiple openings and closings.
- Spilling the hydraulic fluid around the opening while refilling can drag impurities inside
- Through the breather
- While replacing parts in a dirty environment
- Bad gaskets and worn seals allow dirt, microbes, and impurities to work their way in
- Incompatible fittings and hoses can lead to corrosion from leaks and chemical reactions inside the system.
Making sure these entry areas are clean and in good shape will help keep contaminants from reaching your hydraulic fluid lines.
Use the Correct High-Quality Fluids
Hydraulic fluid is your system's lifeblood. Using high-quality, clean hydraulic fluids specifically designed for your machinery can make a world of difference.
Always ensure that the fluid meets the hydraulic system’s specifications and is free from impurities. This will also help prevent leaks and other issues that cause hydraulic system failure.
Use Proper Filtration
Filtration helps catch impurities that make their way into the line before they do damage to your hydraulic system. Invest in high-efficiency filters that can remove 30 microns or smaller impurities from the system. Regularly check and replace these filters according to the manufacturer's recommendations.
Check the Lines if the System Overheats
Extreme temperatures can make the oil too thin and cause metal-to-metal friction in the hydraulic system, leaving metal flakes and sludge in your system. Some of the most common friction related contaminants include:
- Rust
- Minerals
- Metal flakes
- Silica
- Elastomers
When you overwork the system or work in hot conditions, make sure to use additives or a new clean hydraulic oil appropriate for the task.
Use Proper Seals and Breathers
Seals and breathers are critical components in preventing leaks, corrosion, and contamination. Inspect and replace seals regularly to avoid leaks that could let contaminants in. Invest in high-quality breathers that filter out airborne contaminants while allowing the system to breathe properly.
Develop and stick to a maintenance schedule that includes checking these vital parts for signs of wear and corrosion.
Prevent Cross-Contamination
When servicing multiple hydraulic systems, thoroughly clean tools and equipment between uses to prevent cross-contamination. If feasible, use color-coded tools and containers to distinguish between different fluids and systems to reduce the risk of mixing incompatible fluids. Avoid using old fluid in new systems to cut costs.
Implement Contamination Control Programs
Develop and implement comprehensive contamination control programs tailored to your specific hydraulic systems. These programs should include procedures for fluid handling, storage, and disposal, as well as guidelines for maintenance and inspections.
Regularly review and update the program to address new challenges and improve contamination control measures. Make sure to have a number for a hydraulics expert handy in case your team runs into questions or can not identify the source of contaminants.
Action Supply Can Help Minimize Contamination With The Right Parts For the Right Job
The donkey became the company’s symbol because our founders knew they could deliver kick-ass quality — and Action Supply continues to do just that. We’ll help you make sure you are using the right hoses, couplings, and other essential hardware for your hydraulics system every time. We even have a robust inventory management program to ensure your systems do not suffer from extensive back orders. Contact us today to talk to one of our experts.
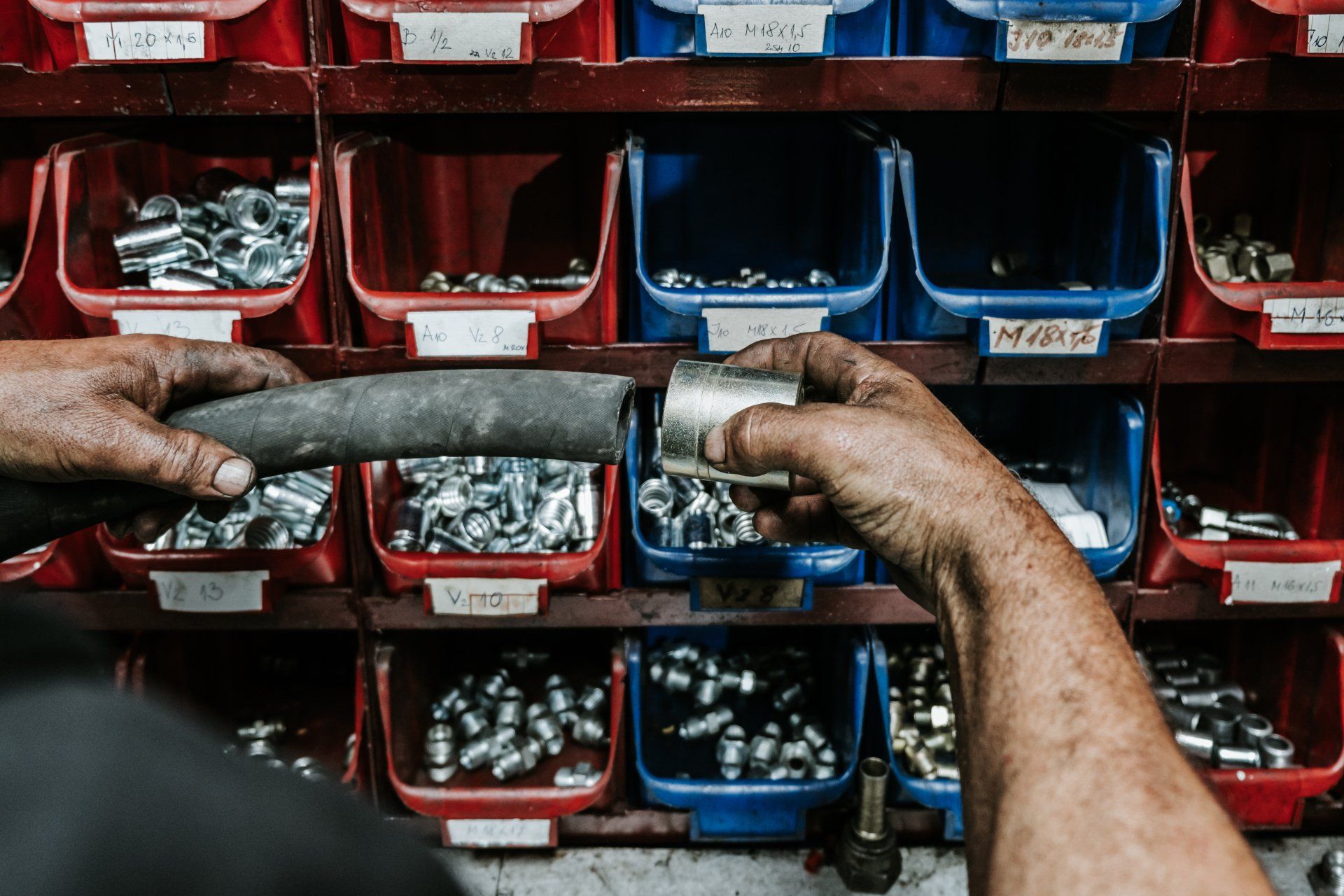
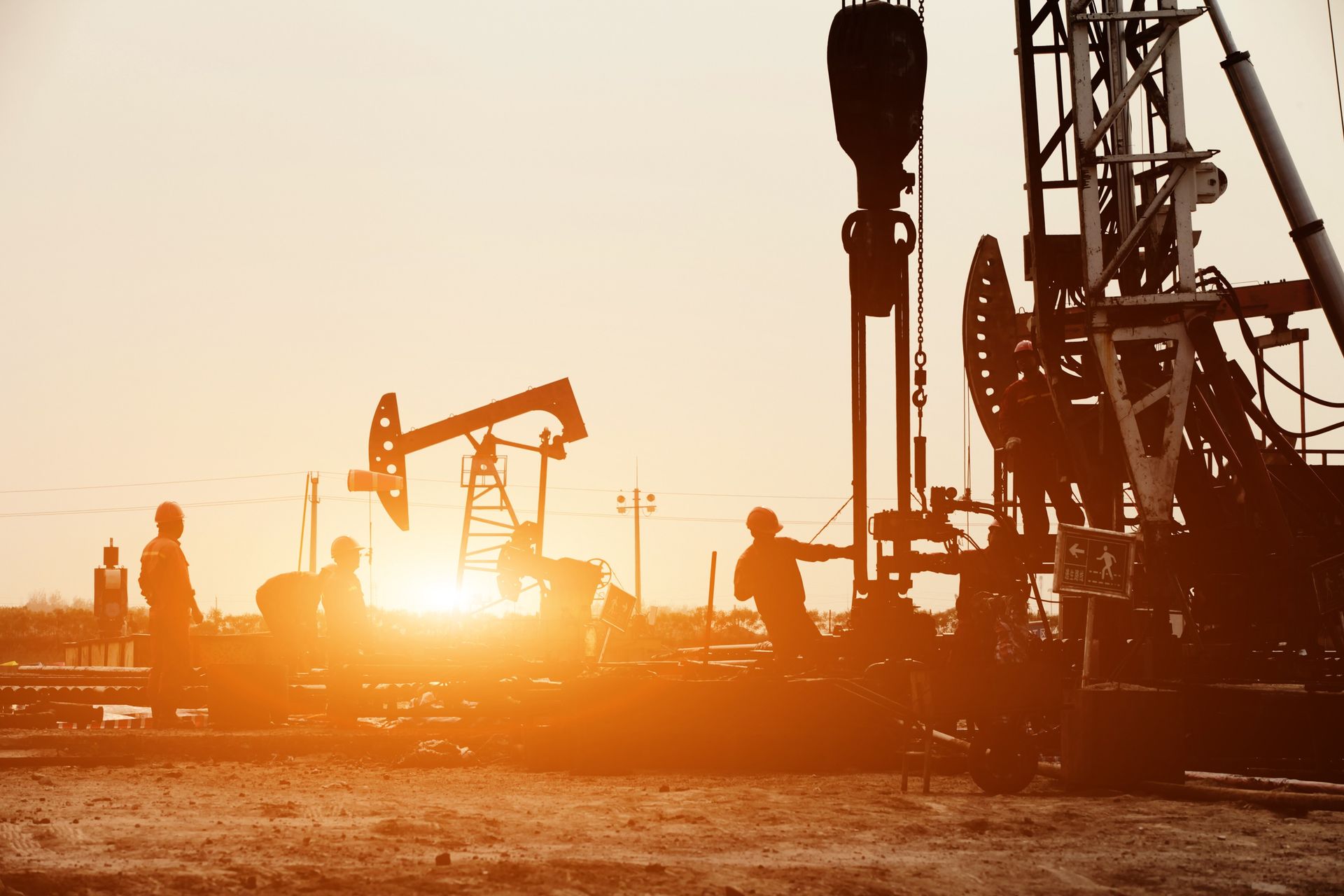